Numerical control technology refers to the technology that uses digital instructions composed of numbers, characters and symbols to control the motion of one or more mechanical equipment. What it controls is usually the position, angle, speed and other mechanical quantities and the switch quantity related to the flow of mechanical energy. The generation of numerical control relies on the emergence of data carriers and binary data operations.
In 1908, the perforated sheet metal interchangeable data carrier came out;
At the end of the 19th century, a control system with paper as a data carrier and auxiliary functions was invented;
In 1938, Shannon conducted rapid data calculation and transmission at the Massachusetts Institute of Technology in the United States, laying the foundation for modern computers, including computer digital control systems. Numerical control technology is developed in close combination with machine tool control.
Numerical control technology originated from the needs of the aviation industry. In the late 1940s, a helicopter company in the United States put forward the initial idea of a CNC machine tool. In 1952, the Massachusetts Institute of Technology developed a three-axis CNC milling machine. This kind of CNC milling machine has been used for processing aircraft parts in the mid-1950s. In the 1960s, numerical control systems and programming work became increasingly mature and perfect. CNC machine tools have been used in various industrial sectors, but the aerospace industry has always been the largest user of CNC machine tools. Some large aviation factories are equipped with hundreds of CNC machine tools, of which cutting machines are the main ones. CNC machining parts include integral wall panels, beams, skins, bulkheads, propellers, and aircraft engine casings, shafts, disks, blades, and special cavity surfaces of liquid rocket engine combustion chambers. . The initial stage of the development of CNC machine tools is mainly based on the continuous track CNC machine tools. Continuous track control is also called contour control, which requires the tool to move in accordance with the specified track relative to the part. Later, we will vigorously develop point-control CNC machine tools. Point control means that the tool moves from one point to another, as long as it can reach the target accurately at the end, regardless of the moving route.
In 1952, the first CNC machine tool came out, which became an epoch-making event in the history of the world machinery industry and promoted the development of automation. Nowadays, numerical control technology is also called computer numerical control technology. At present, it is a technology that uses computers to realize digital program control. This technology uses a computer to execute the control function of the device according to the control program stored in advance. Because the computer is used to replace the original numerical control device composed of hardware logic circuits, the storage, processing, calculation, and logic judgment of the input data can be realized by computer software.
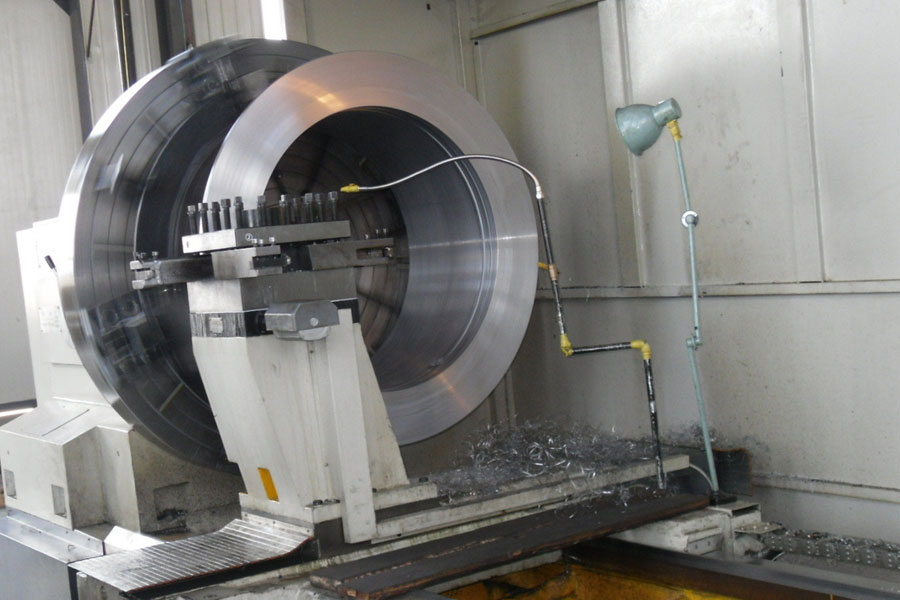
What Is CNC Machining Technology?
Numerical control machining refers to a process method for processing parts on a CNC machine tool. The process regulations of CNC machine tool processing and traditional machine tool processing are generally consistent, but significant changes have also taken place. A machining method that uses digital information to control the displacement of parts and tools. It is an effective way to solve the problems of variable parts, small batches, complex shapes, and high precision requirements, and to achieve high-efficiency and automated processing.
Simply put, it is to use the digital control system to complete the processing of the entire part on the processing machine. This type of machine tool is called CNC machine tool. This is a modern processing method. At the same time, CNC machining technology has also become a symbol of the development of a country’s manufacturing industry. The use of CNC machining technology can complete the machining of many curved parts that could not be completed before, and the accuracy and precision of the machining can be well guaranteed.
A CNC machine tool is a machine tool controlled by a computer. The computer used to control the machine tool, whether it is a special computer or a general-purpose computer, is collectively called a CNC system. The movement and auxiliary actions of the CNC machine tool are controlled by the instructions issued by the CNC system. The instructions of the numerical control system are compiled by the programmer according to the material of the workpiece, the processing requirements, the characteristics of the machine tool, and the instruction format (numerical control language or symbols) prescribed by the system. The numerical control system sends out operation or termination information to the servo device and other functional components according to the program instructions to control various movements of the machine tool. When the part processing program ends, the machine tool will automatically stop. For any kind of CNC machine tool, if there is no program command input in its CNC system, the CNC machine tool cannot work. The controlled actions of the machine tool roughly include the start and stop of the machine tool; the start and stop of the spindle, the conversion of the rotation direction and the speed; the direction, speed, and mode of the feed movement; the selection of the tool, the compensation of the length and the radius; the replacement of the tool, and the cooling The opening and closing of the liquid.
Generally speaking, compared with traditional machining methods, CNC machining technology has the following advantages:
- High processing efficiency. The use of digital control means can process complex curved surfaces. The machining process is controlled by a computer, so the interchangeability of parts is strong and the machining speed is fast.
- High processing precision. Compared with the traditional processing equipment, the numerical control system optimizes the transmission device, improves the resolution, and reduces the human error, so the processing efficiency can be greatly improved. 3. Low labor intensity. Because the automatic control method is adopted, that is to say, the entire processing process is completed by the numerical control system, which is not as cumbersome as the traditional processing means. The operator only needs to monitor the running status of the equipment when working on the numerical control machine tool. So labor intensity is very low.
- Strong adaptability. The CNC machining system is like a computer. It can modify or change its operation mode by adjusting some parameters, so the processing range can be greatly expanded.
- Good working environment. The CNC machining machine tool is a high-tech product of mechanical control, strong current control, and weak current control. It has high requirements on the operating temperature, humidity and environment of the machine tool.
- Easy employment and high remuneration. As my country is in the stage of vigorous development of CNC machining technology, a large number of CNC machine tools and advanced processing methods are rapidly introduced, but there is not a large number of skilled CNC technology operators to participate, resulting in a serious shortage of talents in the industry.
The Operation Process Of CNC Machine Tools
1.CNC Programming
There are manual (manual) programming and automatic programming methods for NC machining programming. Manual programming, the entire content of the program is manually written in accordance with the instruction format specified by the CNC system. Automatic programming is computer programming, which can be divided into automatic programming methods based on language and drawing. However, no matter what kind of automatic programming method is adopted, corresponding hardware and software are required.
It can be seen that the realization of NC machining programming is the key. But programming alone is not enough. CNC machining also includes a series of preparatory work that must be done before programming and the aftermath of programming. Generally speaking, the main contents of CNC machining process are as follows:
- Select and confirm the parts and contents for CNC machining;
- Process analysis of CNC machining of parts drawings;
- Process design of CNC machining;
- Mathematical processing of parts drawings;
- Compile the processing procedure list;
- Make the control medium according to the procedure list;
- Check and modify the program;
- Trial processing of the first piece and on-site problem handling;
- The finalization and filing of CNC machining process documents.
In order to improve the degree of production automation, shorten the programming time and reduce the cost of CNC machining, a series of advanced CNC machining technologies have been developed and used in the aerospace industry. For example, computer numerical control, that is, a small or microcomputer is used to replace the controller in the numerical control system, and the software stored in the computer is used to perform calculation and control functions. This soft-connected numerical control system is gradually replacing the initial state of the numerical control system. Direct numerical control uses one computer to directly control multiple numerical control machine tools, which is very suitable for small batch and short cycle production of aircraft. The ideal control system is an adaptive control system that can continuously change processing parameters. Although the system itself is complex and expensive, it can improve processing efficiency and quality. In addition to the improvement of CNC systems and machine tools in terms of hardware, the development of CNC has another important aspect that is the development of software.
Computer-aided programming (also called automatic programming) means that after a programmer writes a program in numerical control language, it is input into the computer for translation, and finally the computer automatically outputs punched tape or tape. The most widely used CNC language is the APT language. It is roughly divided into a main processing program and a post-processing program. The former translates the program written by the programmer to calculate the tool path; the latter compiles the tool path into the part processing program of the CNC machine tool. Numerical control processing is to write programs on the computer before processing the workpiece, and then input these programs into the machine tool controlled by the computer program for instructional processing, or write instructions directly on the machine tool control panel controlled by the computer program For processing. The machining process includes: tool moving, tool change, speed change, direction change, parking, etc., all of which are completed automatically. CNC machining is an advanced method of modern mold manufacturing and processing. Of course, CNC machining methods must not only be used for mold parts processing, but also have a wide range of uses.
2.Process analysis
The technical issues of CNC machining of the processed parts involve a wide range of aspects. The following combines the possibility and convenience of programming to put forward some main contents that must be analyzed and reviewed.
The dimensioning should conform to the characteristics of CNC machining
In CNC programming, the size and position of all points, lines, and surfaces are based on the programming origin. Therefore, it is best to give the coordinate size directly on the part drawing, or try to quote the size with the same datum.
The conditions of geometric elements should be complete and accurate
In the programming, the programmer must fully grasp the geometric element parameters that constitute the contour of the part and the relationship between the geometric elements. Because all geometric elements of the contour of the part must be defined during automatic programming, the coordinates of each node must be calculated during manual programming. No matter which point is unclear or uncertain, programming cannot be carried out. However, due to inadequate consideration or neglect by part designers in the design process, there are often incomplete or unclear parameters, such as arc and straight line, arc and arc whether they are tangent or intersected or separated. Therefore, when reviewing and analyzing the drawings, you must be careful and contact the designer in time if you find any problems.
Reliable positioning reference
In CNC machining, the machining processes are often concentrated, and it is very important to locate them on the same basis. Therefore, it is often necessary to set some auxiliary datums, or add some process bosses on the blank.
Uniform geometry type or size
It is better to adopt a uniform geometric type or size for the shape and inner cavity of the parts, so as to reduce the number of tool changes, and it is also possible to use control programs or special programs to shorten the program length. The shape of the parts is as symmetrical as possible, which is convenient for programming with the mirror machining function of the CNC machine tool to save programming time.
3.Part Clamping
The basic principles of positioning and installation
When machining parts on a CNC machine tool, the basic principle of positioning and installation is to choose a reasonable positioning datum and clamping plan. Pay attention to the following points when choosing:
- Strive for a unified benchmark for design, process and programming calculations.
- Minimize the number of clamping times, and process all the surfaces to be processed after positioning and clamping once as much as possible.
- Avoid the use of machine-occupied manual adjustment processing schemes to give full play to the effectiveness of CNC machine tools.
The basic principles of choosing fixtures
The characteristics of CNC machining put forward two basic requirements for the fixture: one is to ensure that the coordinate direction of the fixture is relatively fixed with the coordinate direction of the machine tool; the other is to coordinate the size relationship between the parts and the machine coordinate system. In addition, the following points should be considered:
- When the batch of parts is not large, modular fixtures, adjustable fixtures and other general fixtures should be used as much as possible to shorten production preparation time and save production costs.
- Only consider the use of special fixtures during mass production, and strive to have a simple structure.
- The loading and unloading of parts should be fast, convenient and reliable to shorten the machine stop time.
- The parts on the fixture should not hinder the machining of the surface of the parts by the machine tool, that is, the fixture should be open, and its positioning and clamping mechanism components should not affect the knife during processing (such as collisions, etc.).
4.Machining Error
Numerical control machining error △ addition is composed of programming error △ editing, machine tool error △ machine, positioning error △ fixed, tool setting error △ tool and other errors.
Namely: △number plus=f (△editing+△machine+△fixed+△tool)
among them:
- Programming error △ is composed of approximation error δ and rounding error. The approximation error δ is produced in the process of approximating a non-circular curve with a straight line segment or a circular arc segment, as shown in Figure 1.43. The rounding error is the error produced by rounding the coordinate value to an integer pulse equivalent value during data processing. Pulse equivalent refers to the displacement of each unit pulse corresponding to the coordinate axis. Normal-precision CNC machine tools generally have a pulse equivalent value of 0.01mm; more precise CNC machine tools have a pulse equivalent value of 0.005mm or 0.001mm, etc.
- The error of the machine tool is caused by the error of the CNC system and the feed system.
- The positioning error △ is always caused when the workpiece is positioned on the fixture and the fixture is positioned on the machine tool.
- Tool setting error △ tool is generated when determining the relative position of the tool and the workpiece.
The Main Feature Of Cnc Machining
CNC machine tools select aircraft parts with complex profiles as the processing objects from the very beginning, which is the key to solving the difficulty of ordinary processing methods. The biggest feature of CNC machining is to use punched tape (or tape) to control the machine tool for automatic processing. Because airplanes, rockets, and engine parts have different characteristics: airplanes and rockets have zero parts, large component sizes, and complex shapes; engine zero, small component sizes, and high precision. Therefore, the CNC machine tools selected by the aircraft and rocket manufacturing departments and the engine manufacturing departments are different. In aircraft and rocket manufacturing, large-scale CNC milling machines with continuous control are mainly used, while in engine manufacturing, both continuous-control CNC machine tools and point-control CNC machine tools (such as CNC drilling machines, CNC boring machines, machining centers, etc.) are used .
1.Process Concentration
CNC machine tools generally have tool holders and tool magazines that can automatically change tools. The tool change process is automatically carried out under program control. Therefore, the process is relatively concentrated. Process concentration brings huge economic benefits:
- Reduce the floor space of the machine tool and save the workshop.
- Reduce or no intermediate links (such as intermediate inspection of semi-finished products, temporary storage and handling, etc.), which saves time and manpower.
2.Automation
No need to manually control the cutting tools during CNC machine processing, and the degree of automation is high. The benefits are obvious.
- Reduced requirements for operating workers:A senior worker of an ordinary machine tool cannot be trained in a short time, and a CNC worker who does not need programming has a very short training time (for example, a CNC lathe worker needs one week, and he will write simple processing programs). In addition, the parts processed by CNC workers on CNC machine tools have higher precision than those processed by ordinary workers on traditional machine tools, and it takes less time.
- Reduce the labor intensity of workers: CNC workers are excluded from the processing most of the time during the processing, which is very labor-saving.
- Stable product quality: The processing automation of CNC machine tools eliminates the fatigue, carelessness, estimation and other human errors of workers on ordinary machine tools, and improves the consistency of products.
- High processing efficiency: The automatic tool change of the CNC machine tool makes the processing process compact and improves labor productivity.
3.High Flexibility
Although the traditional general-purpose machine tool is flexible, it is inefficient; while the traditional special machine is highly efficient, but has poor adaptability to parts, high rigidity and poor flexibility, and it is difficult to adapt to the fierce competition in the market economy. Products are frequently remodeled. As long as the program is changed, new parts can be processed on the CNC machine tool, and it can be automated, with good flexibility and high efficiency. Therefore, the CNC machine tool can well adapt to market competition.
4.Strong Ability
The machine tool can accurately process various contours, and some contours cannot be machined on ordinary machine tools. CNC machine tools are especially suitable for the following occasions:
- Parts that are not allowed to be scrapped.
- Development of new products.
- Processing of urgently needed parts.
NC Programming
1.Program Structure
A program segment is a continuous group of words that can be processed as a unit, and it is actually a section of a program in a CNC machining program. The main body of the part processing program is composed of several program segments. Most program segments are used to instruct the machine tool to complete or execute a certain action. The block is composed of size words, non-size words and block end instructions. When writing and printing, each block generally occupies one line, and the same is true when the program is displayed on the screen.
2.Program Format
The conventional processing program is composed of the start character (single row one section), the program name (single row one section), the program main body and the program end instruction (generally a single row one section). There is a program end character at the end of the program. The program start character and the program end character are the same character:% in ISO code, ER in EIA code. The program end instruction can be M02 (program end) or M30 (paper tape end). CNC machine tools generally use stored programs to run. At this time, the common point of M02 and M30 is: after completing all other commands in the program segment, they are used to stop the spindle, coolant and feed, and reset the control system. M02 and M30 are completely equivalent when used on some machine tools (systems), but they are different when used on other machine tools (systems): When the program is ended with M02, the cursor stops at the end of the program after the automatic operation ends; and When using M3O to end the program operation, the cursor and screen display can automatically return to the beginning of the program after the automatic operation ends, and the program can be run again by pressing the start button. Although M02 and M30 are allowed to share a block with other program words, it is better to list them in a single block, or share a block with the sequence number only.
The program name is located before the main body of the program and after the start of the program, and it usually occupies a line on its own. The program name has two forms: one is composed of a prescribed English character (multiple use O) at the beginning, followed by several digits. The maximum allowable number of digits is stipulated by the manual, and the two common ones are two digits and four digits. This form of program name can also be called a program number. Another form is that the program name is composed of English characters, numbers or a mixture of English and numbers, and a “-” sign can be added in the middle. This form allows users to name the program more flexibly. For example, the program for the third process of machining the flange with the part drawing number 215 on the LC30 CNC lathe can be named LC30-FIANGE-215-3, which can be used and stored And retrieval, etc. bring great convenience. The form of the program name is determined by the CNC system.
- %
- O1001
- N0 G92 X0 Y0 Z0
- N5 G91 G00 X50 Y35 S500 MO3
- N10 G43 Z-25 T01.01
- N15 G01 G007 Z-12
- N20 G00 Z12
- N25 X40
- N30 G01 Z-17
- N35 G00 G44 Z42 M05
- N40 G90 X0 Y0
- N45 M30
- %
3.Segment Format
The rules for the arrangement of words, characters and data in a program segment are called block format. The fixed sequence format and separator (HT or TAB) block format have been used in the history of CNC. When these two program segment formats have passed, the word address variable program segment format is widely used at home and abroad, also known as the word address format. In this format, the program word length is not fixed, and the number of program words is also variable. Most CNC systems allow the sequence of program words to be arranged arbitrarily, so it belongs to the variable block format. However, in most cases, for the convenience of writing, inputting, checking and proofreading, program words are used to arrange in a certain order in the program segment.
The programming manual of CNC machine tools uses detailed format to classify and stipulate the details of programming: characters used in programming, sequence of program words in the program segment, and word length. E.g:
/ NO3 G02 X+053 Y+053 I0 J+053 F031 S04 T04 M03 LF
The detailed format classification description of the above example is as follows: N03 is the sequence number of the block; G02 indicates that the processing track is a clockwise arc; X+053, Y+053 indicate the end point coordinates of the processed arc; I0, J+053 indicate the processed circle The center coordinate of the arc; F031 is the processing feed rate; S04 is the spindle speed; T04 is the tool number of the tool used; M03 is the auxiliary function command; the LF block end command; / is the skip selection command. The function of the skip selection instruction is: on the premise that the program remains unchanged, the operator can make a choice to execute or not to execute the block in the program that has the skip selection instruction. The method of selection is usually to turn the step selection switch on the operation panel to ON or OFF to realize that the program segment with “/” is not executed or executed.
4.Execute Program
This situation is sometimes encountered when compiling a processing program: a group of blocks appears multiple times in a program, or it is used in several programs. We can extract this group of program segments, name them and store them separately, this group of program segments are subroutines. A subroutine is a section of processing program that can be called by appropriate machine control instructions, and it generally has an independent meaning in processing. The processing program where the instruction to call the subroutine of the first level is located is called the main program. The instruction of the subprogram is also a program segment, which is generally composed of the subprogram call instruction, the name of the subprogram and the number of calls. The specific rules and format vary with the system. For example, it is also “call subprogram No. 55 once”, FANUC system uses ” M98 P55.”, while the American AB system uses “P55x”.
Subroutines can be nested, that is, layer by layer. The relationship between the upper level and the next level is the same as the relationship between the main program and the first level subroutine. The maximum number of layers that can be set depends on the specific CNC system. The form and composition of the subprogram are roughly the same as the main program: the first line is the subprogram number (name), the last line is the “subprogram end” instruction, and the main body of the subprogram is between them. However, the function of the main program end instruction is to end the main program and reset the CNC system. Its instructions have been standardized, and each system uses M02 or M30; and the function of the subprogram end instruction is to end the subroutine and return to the main program or the previous subroutine. , The commands are not unified in each system, such as M99 for FANUC system, M17 for Siemens system, M02 for system of American A-B company, etc.
User macros (programs) can be used in CNC machining programs. The so-called macro program is a subprogram that contains variables. The instruction that calls the macro program in the program is called the user macro instruction, and the function that the system can use the user macro program is called the user macro function. When executing, you only need to write the user macro command to execute its user macro function.
The biggest features of user macros are:
● Variables can be used in user macros;
●Can use calculation formulas, turning statements and various functions
●You can use user macro commands to assign values to variables.
The CNC machine tool adopts group technology to process parts, which can expand the batch size, reduce the amount of programming, and improve economic efficiency. In group processing, the parts are classified, and the processing program is compiled for this type of parts, instead of editing a program for each part. When processing the same type of parts with different sizes, the main convenience of using user macros is that you can use variables to replace specific values. When actually processing, you only need to assign the actual size values of this part to variables with user macro commands.
The Principle Of Cnc Machining
- The processing of the previous process cannot affect the positioning and clamping of the next process.
- First inside and then outside, that is, the inner cavity (inner hole) is processed first, and then the outer shape is processed.
- The process of machining with the same installation or using the same tool should be carried out continuously to reduce errors caused by repositioning or tool change.
- In the same installation, the process that has little effect on the rigidity of the workpiece should be carried out first.
1.Processing Route
The feed processing route of the CNC lathe refers to the path that the turning tool moves from the tool setting point (or the fixed origin of the machine tool) until it returns to this point and ends the processing program, including the path of cutting and the path of the tool cutting people, cutting out, etc. Cut the empty stroke path.
The feed route of finishing is basically carried out along the part contour sequence. Therefore, the focus of determining the feed route is to determine the feed route of rough machining and idle stroke.
In CNC lathe processing, the determination of the processing route generally follows the following principles.
- It should be able to guarantee the accuracy and surface roughness of the workpiece to be processed.
- Make the processing route the shortest, reduce the idle travel time, and improve the processing efficiency.
- Simplify the workload of numerical calculation as much as possible and simplify the processing procedure.
- For some reusable programs, subroutines should be used.
Making the machining program have the shortest feed route can not only save the execution time of the entire machining process, but also reduce unnecessary tool consumption and wear of the sliding parts of the machine tool’s feed mechanism. The type and realization method of the shortest feed path are as follows.
⑴ The shortest cutting feed route.
The shortest cutting feed path can effectively improve production efficiency and reduce tool loss. When arranging the shortest cutting feed route, it is also necessary to ensure the rigidity of the workpiece and the requirements of processing technology.
⑵ The shortest empty trip route.
- Use the starting point skillfully. An example of a general situation of rough turning using rectangular loop mode. The setting of tool setting point A is to take into account the need for convenient tool change during finishing turning and other machining processes, so it is set at a position far away from the blank, and at the same time, the starting point and the tool setting point are overlapped.
- Carefully set the tool change point. In order to consider the convenience and safety of tool change, sometimes the tool change point is also set far away from the blank.Position, then, when the second tool is changed, the idle stroke path during finishing turning must be longer; if the tool change point of the second tool is also set at the middle position, the idle stroke can be shortened. Travel distance.
- Reasonably arrange the “return to zero” route. In order to simplify the calculation process and facilitate the verification when manually compiling the processing program of the complex contour, the programmer sometimes returns the end point of the tool after each tool is processed by executing the “return to zero” operation instruction to make it all return to the tool setting point Position, and then perform subsequent procedures. This will increase the distance of the feed path and reduce production efficiency. Therefore, when rationally arranging the “return to zero” route, the distance between the end point of the previous cut and the start point of the next cut should be as short as possible. Or zero to meet the shortest feed path requirement. In addition, when selecting the command to return to the tool setting point, under the premise of no interference, use the x and z-axis bidirectional “zero return” command as much as possible. The function “zero return” route is the shortest.
⑶ Step cutting feed route for large margin blanks.
The cutting progress of two kinds of blanks with too much margin are listed.
Give the route. It is the wrong step cutting route. Cut in the order of 1 bucket and 5, and the margin left for each cutting is equal, which is the correct step cutting feed route. Because under the same amount of knife back.
⑷Continuous cutting feed route for finishing part contour.
The finishing of the contour of the part can be arranged with one or several finishing processes. The finished contour should be continuously processed by the last cut. At this time, the tool’s forward and backward positions should be selected appropriately. Try not to arrange cutting and cutting out or tool change and pause in the continuous contour, so as to avoid sudden changes in cutting force. And destroy the equilibrium state of the process system. Cause scratches, shape mutations or retained tool marks on the contour of the part.
⑸Special feed route.
In CNC turning processing, under normal circumstances. The longitudinal feed of the tool is fed along the negative direction of the coordinate, but sometimes it is unreasonable to arrange the feed route according to its normal negative direction. It may even damage the workpiece.
The Advantages And Disadvantages Of CNC Machining
CNC machining has the following advantages:
- The number of tooling is greatly reduced, and complex tooling is not required for processing parts with complex shapes. If you want to change the shape and size of the part, you only need to modify the part processing program, which is suitable for new product development and modification.
- The processing quality is stable, the processing precision is high, and the repeat accuracy is high, which is suitable for the processing requirements of the aircraft.
- The production efficiency is higher in the case of multi-variety and small-batch production, which can reduce the time of production preparation, machine tool adjustment and process inspection, and reduce the cutting time due to the use of the best cutting amount.
- It can process complex profiles that are difficult to process by conventional methods, and even process some unobservable processing parts. The disadvantage of CNC machining is that the cost of machine tools is expensive and requires a high level of maintenance personnel.
Link to this article:Cnc Machining
Reprint Statement: If there are no special instructions, all articles on this site are original. Please indicate the source for reprinting.:Cnc Machining,Thank!^^